Cutting-edge Techniques to Fillet Weld Evaluation and Testing: Enhancing Weld Top Quality and Conformity Criteria
In the world of welding, the high quality and integrity of fillet welds play a critical duty in making certain the architectural sturdiness and reliability of various commercial components. With the consistent drive for enhanced efficiency and conformity with rigid requirements, the expedition of ingenious methods to fillet weld inspection and screening has come to be critical.
Advanced Non-Destructive Screening Techniques
Making use of advanced technologies, progressed non-destructive testing methods play an essential duty in making sure the stability and quality of fillet welds. These approaches, such as phased variety ultrasonic testing (PAUT) and magnetic bit testing (MPT), offer thorough insights right into the weld's internal structure without creating any damages to the product. PAUT, as an example, uses multiple ultrasonic aspects to evaluate the weld from various angles, giving an extensive visualization of possible issues like lack of blend or cracks.
Likewise, MPT works in spotting surface-breaking flaws by using an electromagnetic field and iron bits to the weld location. This approach is specifically valuable for recognizing gaps that might compromise the weld's strength. By utilizing these innovative non-destructive screening techniques, weld inspectors can precisely examine the top quality of fillet welds, ensuring compliance with industry standards and policies. The capability to identify flaws early not just boosts weld top quality but likewise avoids pricey rework or failures in structural integrity, highlighting the importance of these ingenious testing techniques in welding examinations.
Robotics and Automation in Examination

The combination of robotics and automation has actually revolutionized the examination procedure for fillet welds, enhancing performance and accuracy in quality analysis. Robotics provide specific control and repeatability in evaluating welds, making sure trusted and constant outcomes. Automated systems can be configured to follow details assessment paths, making certain thorough protection of welds and decreasing the threat of human error.
Robotic inspection systems furnished with advanced sensors can find and gauge weld features with high precision, supplying detailed data for analysis. These systems can determine issues such as cracks, lack of blend, and porosity, making it possible for prompt corrective actions to be taken. Furthermore, robotics and automation permit real-time information collection and evaluation, giving immediate feedback to operators and helping with fast decision-making procedures.
Moreover, using robotics and automation in fillet weld examination improves total productivity by reducing inspection times and enhancing evaluation throughput. By improving the evaluation process, producers can guarantee weld quality and compliance criteria are fulfilled successfully, eventually causing cost savings and enhanced item high quality.
Using Artificial Intelligence for Analysis
Artificial knowledge plays an essential function in improving the efficiency and precision of analysis in fillet weld assessment processes. By taking advantage of the power of AI, examiners can simplify the evaluation of weld high quality and compliance criteria, resulting in much more reliable and specific outcomes. AI algorithms can swiftly process vast quantities of data from weld examinations, identifying flaws or disparities that might be challenging to relate to the naked eye. This innovative innovation enables real-time surveillance of weld quality, permitting for instant rehabilitative actions to be taken if any kind of issues are found.
Moreover, AI systems can pick up from previous evaluation data, constantly improving their capability to determine possible defects and variances in fillet welds. This flexible learning ability their explanation improves the general quality assurance process, decreasing the likelihood of human error and making sure that welds fulfill the called for standards. By see this site integrating man-made knowledge right into fillet weld evaluation, sectors can attain greater degrees of performance, uniformity, and conformity in their assessment techniques.
Portable Devices for On-Site Examination
Enhancing area examination efficiency, the adoption of portable devices revolutionizes on-site evaluation procedures for fillet welds. These devices supply adaptability and ease, permitting assessors to perform detailed exams in numerous places, including remote or challenging settings. Mobile tools such as ultrasonic testing tools, magnetic fragment assessment devices, and digital radiography systems give real-time information and high-resolution imaging abilities, enabling fast decision-making and prompt comments on weld high quality.
One substantial advantage of portable tools is their capacity to improve inspection treatments, reducing downtime and improving overall efficiency - Gauge Fillet Weld. Assessors can quickly transfer these tools to different job websites, removing the need for carrying hefty machinery or components to off-site facilities. Additionally, the portability of these tools advertises cost-effectiveness by decreasing transport expenses and increasing assessment timelines
In addition, using portable tools for on-site inspection promotes positive quality assurance measures, as assessors can promptly recognize and attend to any kind of possible welding defects or disparities. By incorporating these ingenious modern technologies right into on-site assessment practices, welding specialists can guarantee compliance with sector requirements and enhance weld high quality, eventually resulting in boosted structural integrity and safety in different welding applications.
Assimilation of Data Monitoring Systems
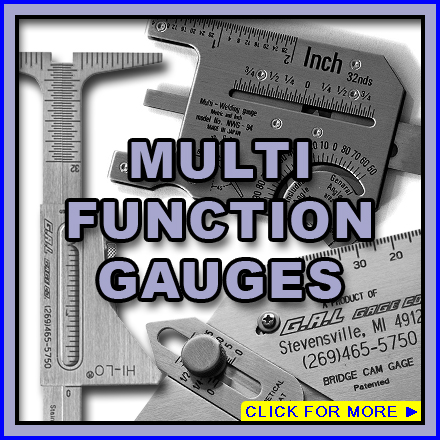
Having optimized on-site examination processes through the usage of portable devices, the following phase entails the seamless integration of information management systems to better enhance effectiveness and information analysis capabilities in fillet weld inspection and screening. By integrating data monitoring systems into the evaluation process, companies can improve information collection, storage space, and evaluation. This integration enables real-time monitoring of weld top quality, immediate recognition of problems, and prompt decision-making to fix any problems that might occur throughout the evaluation procedure.
The combination of data management systems enables smooth interaction in between different stakeholders included in the evaluation process, cultivating cooperation and improving general quality control measures. Inevitably, the assimilation of data management systems offers to raise the requirements of fillet weld inspection and screening, making sure compliance with industry guidelines and improving weld quality.
Verdict
To conclude, innovative approaches to fillet weld examination and screening have significantly boosted weld high quality and compliance criteria. Advanced non-destructive testing approaches, robotics, automation, expert system, mobile tools, and information management systems have actually transformed the means weld evaluations are performed. By using these modern technologies, markets can make certain that welds satisfy the called for quality criteria and regulations, eventually boosting general performance and safety in welding processes.

Having optimized on-site examination procedures through the application of portable tools, the following phase entails the seamless integration of information management systems to better improve efficiency and information analysis capacities in fillet weld assessment and testing. Inevitably, the combination of information monitoring systems serves to elevate the criteria of fillet weld evaluation and screening, guaranteeing conformity with industry guidelines and enhancing weld high quality.
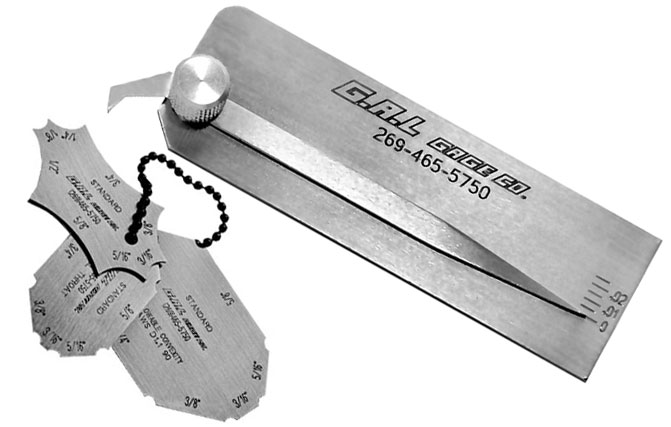